General e-lab description
ACS-850 online laboratory work is based on the existing offline lab work used in the study process in the “ATV0080 Supply converters and control of machines” course at the Tallinn University of Technology (TalTech, Estonia). The work is based on the ABB ACS850-04 demo suitcase and involves testing and adjusting the ACS850 frequency converter to ensure the proper functioning and understanding of the principle of operation. The work aim is to learn how to:
- Control constant speeds/direction of rotation,
- Adjust acceleration and deceleration modes,
- Use of digital and analog inputs,
- Implement IR compensation and other industrial frequency converter features.
In the laboratory work, real hardware is used, bringing students’ study experience closer to real life. The lab is integrated into Moodle, so all the lab-related materials, report templates, and manuals can be accessed. Via the links, students may connect to the actual hardware setup, control it and observe the information using both the user interface (UI) and camera stream.
Description of the tools and hardware
The drive of the ACS850-04 demo suitcase is modified to suit the single-phase supply. The demo suitcase drive has firmware tailored for 230 VAC single-phase supply. The suitcase is provided with an ABB M2VA 56 B 4 asynchronous machine [1]. With the support of the firmware program, it is possible to maintain the control functions and control the speed and torque. Parameter settings are essential for firmware functions configuring and programming. Parameter settings can be programmed via the control panel, the DriveStudio PC tool, or the Fieldbus interface. Parameters are programmed in the drive to change specific settings of the drive. ABB ACS-850 frequency converter has up to 99 parameter groups. ABB ACS-850 can be connected to an external control system via an embedded Fieldbus interface, supporting Modbus RTU protocol. Both are sending and receiving cyclic data is possible with this protocol with a 10 ms time level. XD2D connection terminals on the JCU control unit can be used to communicate with the device via the Embedded Fieldbus interface (RS-485)[2].
The presence of the RS-485 communication interface and Modbus TRU protocol were the main reasons for selecting the Raspberry Strato Pi CAN module. Strato Pi CAN is a Raspberry Pi 4-based server for industrial and automotive applications. The module is equipped with CAN V2.0B and RS485 interfaces which enable communication with industrial equipment. Also, Strato Pi is equipped with a hardware watchdog, a real-time clock (RTC) equipped with a replaceable backup battery, a pre-assembled cooling system, and a relay with change-over (CO) [3].
The UI to control the hardware setup is a website created using CSS, HTML, and JavaScript languages. The website-based UI has the same functionality as the control panel of the ACS-850 converter but is adapted to the web page. Certain interface modules are implemented using a Bootstrap free and open-source CSS framework.
Table 1. Hardware description
Nr | Device | Task |
1 | ACS850-04 demo suitcase | The system being controlled |
2 | Strato Pi CAN server | Server for the web page-based UI, control of the system Communication with the lab system |
3 | Raspberry Pi 4 | Server for the web page-based UI, video streaming |
4 | Logitech C615 web camera | Producing the video stream |
Working principle
Strato Pi CAN board constantly reads the values from the holding registers of ACS-850 using the RS-485 interface and Modbus communication protocol. The back-end code is written in Python using Modbus Test Kit and OpenCV libraries. This solution allows the user to access only specific registers defined within the code to control the lab setup. It is done to optimize the use of computational resources, as a constant reading of all the registers may be inefficient. The front-end solution is created using the CSS, HTML, and JavaScript languages. Some UI modules were done using a Bootstrap free and open-source CSS framework. The data exchange between the front-end and back-end is one using JSON files.
The website-based UI has the same functionality as the control panel of the ACS-850 converter but is adapted to the web page and e-lab requirements. The user can obtain the lab setup’s real-time condition and control it by observing the changing values via the UI.
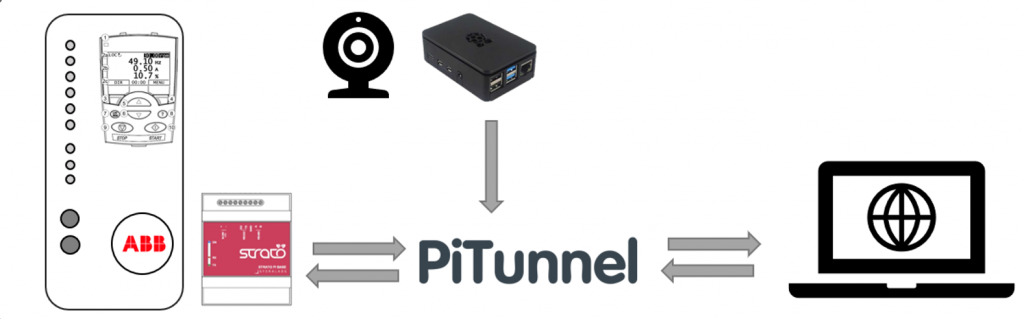
Fig. 1 System structure
If you are interested in taking advantage of the laboratory’s offer, please contact the project leader or staff of the Electrical Machine Group at Tallinn University of Technology – leader of the O2 output.
[1] “3GVA052002-CSA | ABB.” https://new.abb.com/products/3GVA052002-CSA/3gva052002-csa (accessed Jan. 04, 2023).
[2] “ACS850 Firmware Manual ACS850 Standard Control Program.”
[3] “Strato Pi – The Industrial Raspberry Pi – Sfera Labs.” https://www.sferalabs.cc/strato-pi/ (accessed Jan. 04, 2023).